What is Porosity in Welding: Understanding Its Causes and Enhancing Your Skills
What is Porosity in Welding: Understanding Its Causes and Enhancing Your Skills
Blog Article
Unwinding the Enigma of Porosity in Welding: Tips for Reducing Defects and Making The Most Of Quality
In the intricate globe of welding, porosity stays a persistent difficulty that can significantly affect the high quality and honesty of welded joints. Understanding the variables that add to porosity formation is essential in the quest of remarkable welds. By unwinding the secret of porosity and implementing efficient methods for issue minimization, welders can elevate the criteria of their job to attain remarkable quality outcomes. As we explore the depths of porosity in welding, revealing the tricks to its avoidance and control will certainly be critical for specialists looking for to grasp the art of premium weldments.
Recognizing Porosity in Welding
Porosity in welding, a typical concern experienced by welders, describes the visibility of gas pockets or voids in the bonded material, which can compromise the honesty and quality of the weld. These gas pockets are usually entraped during the welding procedure as a result of various factors such as inappropriate protecting gas, infected base products, or inaccurate welding criteria. The development of porosity can weaken the weld, making it at risk to breaking and deterioration, ultimately causing structural failings.
Comprehending the source of porosity is vital for welders to effectively prevent its event. By identifying the significance of maintaining appropriate gas protecting, making sure the tidiness of base products, and enhancing welding setups, welders can significantly minimize the chance of porosity formation. In addition, making use of methods like pre-heating the base product, utilizing appropriate welding techniques, and performing extensive examinations post-welding can additionally aid in lessening porosity issues. Generally, a comprehensive understanding of porosity in welding is important for welders to create high-quality and long lasting welds.

Usual Root Causes Of Porosity
When examining welding processes for prospective top quality problems, comprehending the common causes of porosity is essential for preserving weld integrity and preventing architectural failures. Porosity, identified by the visibility of cavities or spaces in the weld metal, can substantially compromise the mechanical residential properties of a welded joint.
One more widespread reason of porosity is the presence of dampness and pollutants externally of the base steel or filler material. When welding products are not effectively cleaned or are revealed to high degrees of moisture, the evaporation of these pollutants throughout welding can create gaps within the weld bead. In addition, welding at incorrect parameters, such as exceedingly high travel speeds or currents, can create extreme disturbance in the weld swimming pool, trapping gases and causing porosity. By resolving these typical reasons through correct gas shielding, material prep work, and adherence to optimal welding specifications, welders can lessen porosity and enhance the high quality of their welds.
Methods for Porosity Prevention
Applying effective safety nets is critical in lessening the occurrence of porosity in welding processes. One strategy for porosity avoidance is making certain correct cleansing of the base steel before welding. Impurities such as oil, oil, rust, and paint can bring about porosity, so extensive cleansing utilizing proper solvents or mechanical methods is vital.

Making use of high-quality filler materials and shielding gases that are ideal for the base metal and welding process can significantly minimize the threat of porosity. Furthermore, preserving appropriate welding parameters, look what i found such as voltage, existing, take a trip rate, and gas flow price, is essential for porosity prevention.
Furthermore, employing proper welding strategies, such as maintaining a consistent traveling speed, electrode angle, and arc size, can assist protect against porosity (What is Porosity). Ample training of welders to ensure they comply with best methods and quality assurance procedures is likewise important in minimizing porosity issues in welding

Ideal Practices for High Quality Welds
Guaranteeing adherence to market requirements and proper weld joint prep work are fundamental facets of achieving consistently high-grade welds. Along with these fundamental steps, there are a number of finest practices that welders can apply to additionally boost the quality of their welds. One secret practice is keeping appropriate tidiness in the welding area. Contaminants such as oil, oil, rust, and paint can negatively impact the quality of the weld, bring about issues. Extensively cleaning up the workpiece and surrounding area before welding can assist mitigate these issues.
One more ideal method is to meticulously pick the appropriate welding parameters for the certain products being joined. This includes setting the proper voltage, present, take a trip speed, and securing gas flow rate. Correct criterion option guarantees ideal weld penetration, combination, and overall quality. Making use of top notch welding consumables, such as electrodes and filler steels, can significantly impact the last weld top quality. Spending in premium consumables can lead to stronger, much more resilient welds with less defects. By adhering to these ideal methods, welders can continually produce premium welds that meet sector standards and exceed consumer expectations.
Importance of Porosity Control
Porosity control plays an essential role in ensuring the stability and quality of welding joints. Porosity, characterized by the visibility of tooth cavities or voids within the weld steel, can considerably jeopardize the mechanical properties and architectural stability of the weld. Extreme porosity weakens the weld, making it more vulnerable to cracking, corrosion, and general failure under operational tons.
Effective porosity control is vital for preserving the preferred mechanical properties, such as stamina, ductility, and durability, of the bonded joint. What is Porosity. By you can try these out reducing porosity, welders can enhance the overall quality and reliability of the weld, guaranteeing that it fulfills the efficiency requirements of the desired application
Moreover, porosity control is essential for accomplishing the preferred visual look of the weld. Extreme porosity not just damages the weld yet also takes away from its visual charm, which can be essential in sectors where more tips here aesthetics are essential. Proper porosity control strategies, such as making use of the proper shielding gas, managing the welding specifications, and making certain correct cleanliness of the base materials, are vital for creating high-grade welds with marginal defects.
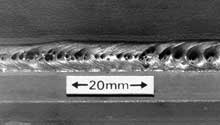
Verdict
Finally, porosity in welding is a common flaw that can jeopardize the top quality of the weld. By comprehending the root causes of porosity and applying appropriate prevention methods, welders can minimize flaws and accomplish greater high quality welds. It is vital to manage porosity in welding to guarantee the honesty and strength of the final item. Carrying out ideal practices for porosity control is vital for attaining optimal welding outcomes.
Report this page